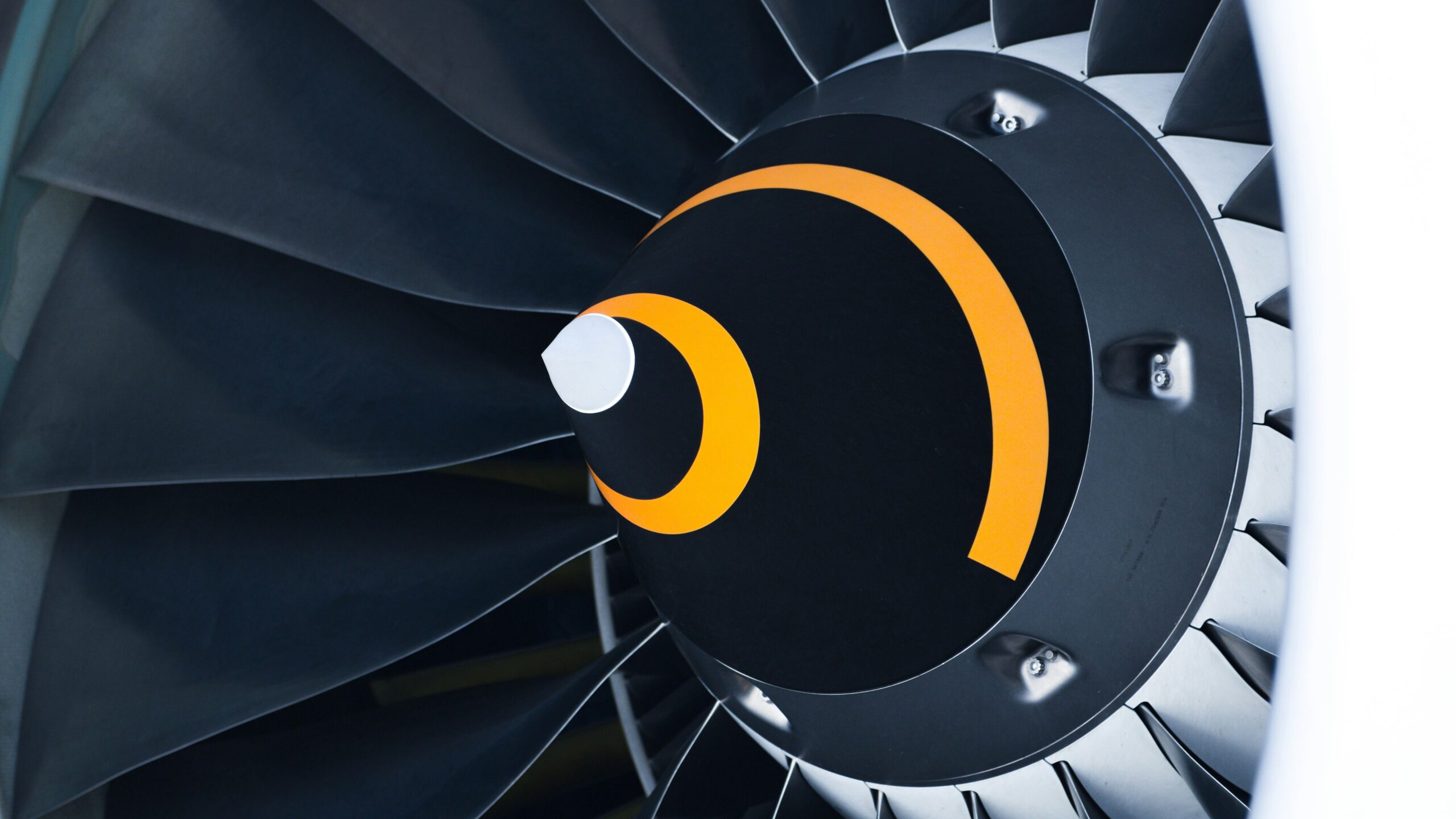
Eliminate the environmental impact of aviation
In 2019, before the COVID-19 pandemic, commercial aviation carried more than 4.5 billion passengers and moved around 61 million tonnes of cargo. This volume of air traffic, driven by globalisation and increased mobility, has led to an average annual growth of 5% in flight demand. Commercial and cargo aviation is a major source of greenhouse gas emissions. Although 2-3% of global carbon dioxide emissions may sound like a small percentage, aviation's contribution to climate change is larger due to the combined effects of other emissions, such as nitrogen oxides (NOx), and atmospheric phenomena associated with aircraft, such as contrails and "artificial" clouds induced by air traffic. Aircraft engines emit NOx, gases which, in addition to being highly polluting, contribute to changes in the concentration of methane and tropospheric ozone, both of which are potent greenhouse gases. At lower altitudes, NOx emissions also lead to degradation of air quality, which directly affects human health and natural ecosystems.
Condensation trails (technically called condensation trails) also come into play. contrailsno chemtrails as many conspiracy theories suggest), a kind of "artificial clouds" that form when water vapour from engine exhaust condenses into small aerosol particles in the atmosphere, creating thin cloud trails. These contrails can become persistent and evolve into cirrus clouds, which have a net warming effect due to their ability to reflect and trap infrared radiation emitted by the earth's surface. In summary, pollutants emitted by aviation, such as CO₂, NOx, water vapour and aerosol particles, contribute to global warming. The increasing demand for flights translates into indirect growth in emissions due to the need to extract more fuel, the expansion of airport infrastructure and airspace congestion. The Intergovernmental Panel on Climate Change (IPCC) estimates that aviation's total impact on climate change is approximately twice that caused by its direct carbon dioxide emissions, due to these combined effects.
During the pandemic, CO₂ emissions from aviation decreased significantly due to reduced flights and travel restrictions, providing a unique opportunity to assess the environmental impact of aviation and reflect on strategies for sustainable recovery. For example, post-pandemic recovery strategies can serve as a catalyst for investment in cleaner and more efficient aviation technologies. On the one hand, airlines and aircraft manufacturers can accelerate the adoption of alternative propulsion technologies and sustainable fuels, and on the other hand, governments and international organisations can implement policies that promote sustainability in aviation, such as incentives for the use of sustainable fuels, stricter emissions regulations and financial support for research and development. This chapter reviews some of the most interesting proposals.
Before considering possible solutions to decarbonise the aviation industry, it is reasonable to examine some of the most important challenges. Perhaps one of the main problems is the extremely high dependence on paraffin as a fuel. This liquid substance, which is somewhat more viscous than gasoline, has a very high energy density: it releases a lot of energy when burned, in proportion to the volume it occupies, and this is ideal for air transport, especially over long distances. However, burning paraffin produces CO2 and, in addition, it is a fossil fuel and therefore finite. We need alternative solutions that are not only clean and less polluting but also sustainable and renewable.
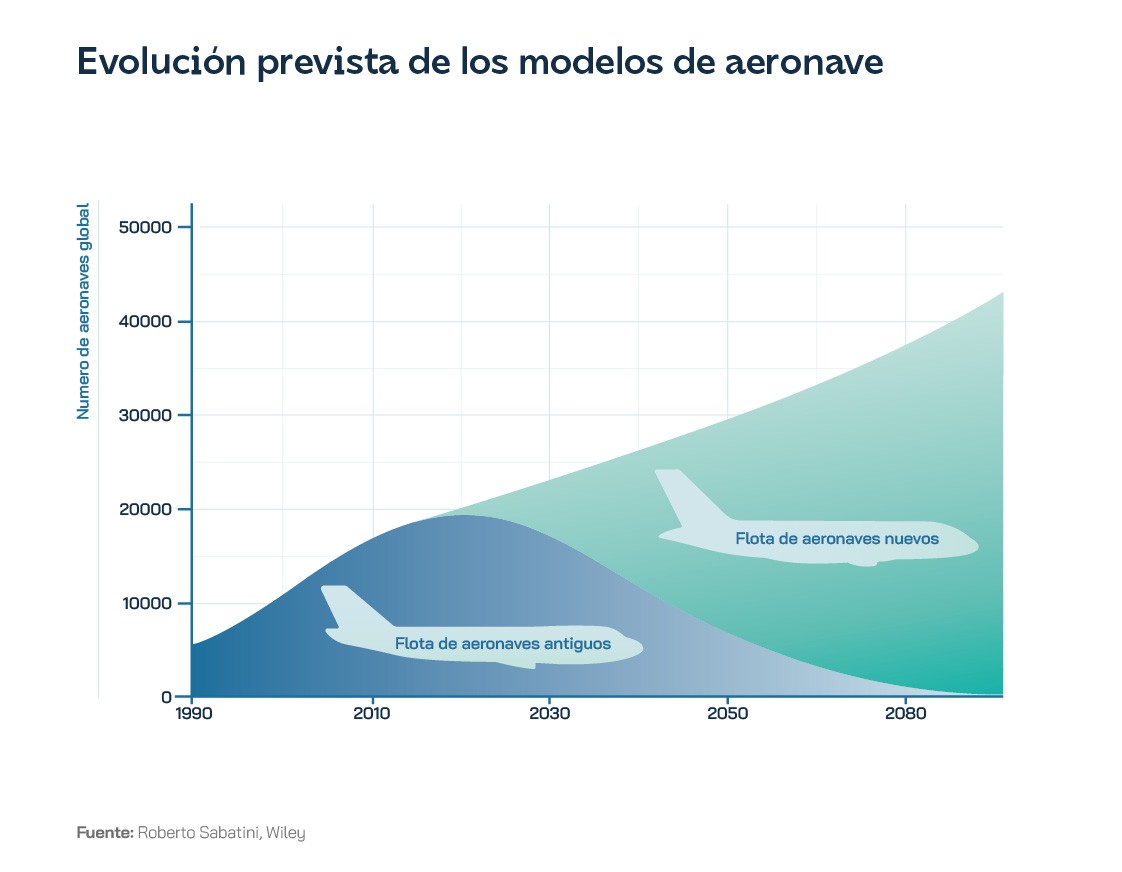
Another problem of the aviation industry is the complexity of its infrastructures, not only because of the large investments required for the development and implementation of new solutions, but also because of the barriers imposed by regulations and standards. For safety reasons, even the smallest change to an aircraft can take years, even decades, to reach a commercial application. It is therefore essential to start new technological developments as soon as possible in order to be able to adopt the changes effectively. Modernisation (and decarbonisation) requires the adoption of new regulatory models that facilitate and accelerate decision-making on sustainable solutions.
One of the most accessible in this regard is the development of new fuels that are more sustainable than paraffin. Although we review many of these alternatives in the chapter on clean fuels, it is worth highlighting some of the most interesting innovations in this sector, popularly known as SAFs (Sustainable Aviation Fuels). Some of the most optimistic estimates calculate that SAFs could reduce carbon dioxide emissions by up to 95%. However, it is important to consider the origin of these fuels. Some alternatives such as biofuels (derived from feedstocks such as sugar, vegetable oils, animal fats and agricultural residues) pose challenges related to long-term sustainability and competition with food production. A perhaps more interesting option is fully synthetic fuels, produced by mimicking plants from atmospheric CO₂ and renewable energies, a solution often referred to as artificial photosynthesis or "power-to-liquid". The main challenges, in this case, are technological. Although this technology is ready to operate at laboratory scales, it is still too early to produce fuels in the quantities needed and regularly used by the aviation industry. We would also need to improve the current capacity for carbon capture, so that we can harness excess CO₂ in the atmosphere as a renewable and circular feedstock. There are many ambitious initiatives in this regard, including the industrial "Mamooth" plant designed and built by Climeworks in Iceland, ten times the size of its former "Orca" plant. This plant plans to capture 36,000 tonnes of CO₂ - the equivalent of the annual emissions of 2,500 people. This is a very promising and positive start.
Among the various technological solutions to decarbonise aviation, electric and hybrid engines represent a significant advance, as in the automotive industry. These propulsion systems could achieve flights with lower emissions and, in the case of electric engines, it is possible to envisage flights completely free of direct emissions (provided that the electricity comes from renewable sources). Electric motors, on the one hand, work by converting electrical energy, usually stored in batteries, into mechanical energy. This technology is particularly attractive for short-haul flights and small aircraft. Electric motors have the advantage of being more efficient and less noisy than internal combustion engines. They also tend to require less maintenance because they have fewer moving parts. However, their deployment (and success) depends on the energy density of today's batteries. Lithium-ion batteries, the most commonly used, cannot store enough energy for long-haul flights without adding considerable weight. For example, some prototypes in small (20-passenger) aircraft for short trips of up to 400 kilometres weigh 3.5 tonnes, which is unacceptable for larger aircraft. Batteries also pose many safety challenges: many lithium-ion batteries are currently banned from aircraft holds because of the risk of short circuits and spontaneous fires. Despite these challenges, research into high energy density batteries, such as solid-state batteries, could offer miracle solutions in the future.
Hybrid propulsion systems, on the other hand, combine internal combustion engines with electric motors, providing greater flexibility and efficiency. These systems can operate in pure electric mode during take-off and landing, where fuel consumption is higher and emissions are more critical (and, in addition, the power of the electric motor can facilitate manoeuvring), and in internal combustion mode during cruise, where fuel efficiency is higher. This combination reduces both emissions and fuel consumption. In addition, hybrid engines, as in cars, can recover part of the energy generated during descent and braking, which can be stored in batteries. However, the integration of electric and hybrid systems is complex and requires very different designs and developments to current aircraft, something that could slow adoption by major manufacturers. Some companies, such as Rolls Royce, have shown promising results: they are studying pilot systems in small aircraft such as helicopters, with interesting and potentially scalable results.
Hydrogen is another emerging technology with significant potential to decarbonise aviation. As a fuel, hydrogen has a lower energy density (by volume) than fossil fuels, but is somewhat more versatile: it can be used either as an energy source in fuel cells, to generate electricity, or directly as a fuel in modified combustion engines. Fuel cells, for example, offer far greater capacity than batteries, and could allow longer-range flights with zero emissions. On the other hand, hydrogen can also be burned directly in combustion engines, to take advantage of existing engine and airfield infrastructure with certain adaptations. However, the adoption of hydrogen faces technical and economic challenges, as we review in the INTEC 2021 report, including issues related to safe storage and the infrastructure needed for its distribution, which has very different requirements than traditional fuels. Despite this, hydrogen represents a key opportunity for emission-free long-range aviation, and several projects and prototypes, both public and private, are currently under development. For example, the German company H2Fly conducted a demonstration of the first liquid hydrogen flight in 2023, and other companies in the US followed suit with several highly successful trials.
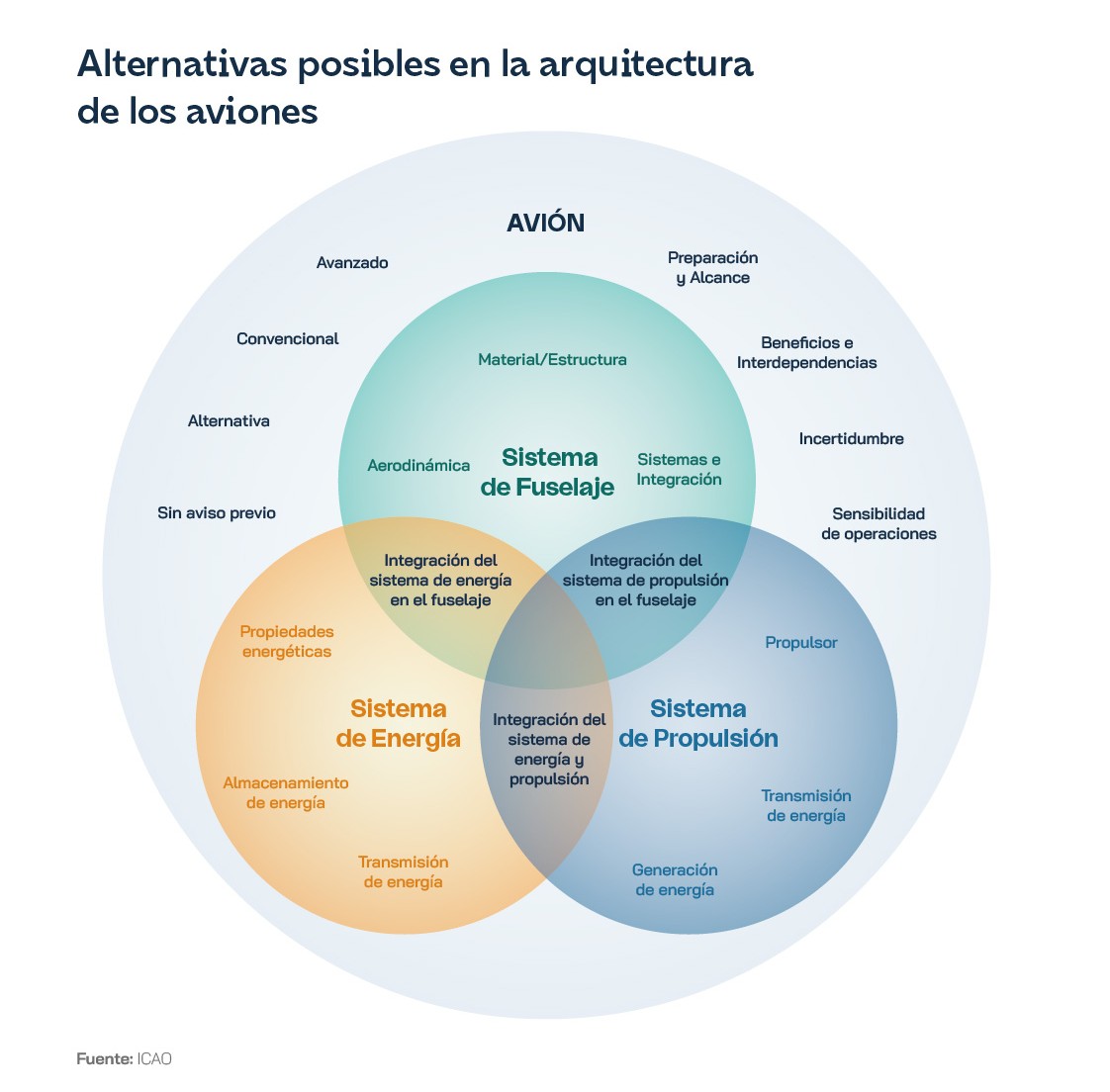
In addition to innovations in propulsion systems, the development of new materials and advanced aircraft design can play a crucial role in reducing aviation emissions towards a more sustainable transport solution. First, new materials and composite materials (also commonly known as "composites") are revolutionising the aviation industry. These materials, such as carbon fibre and graphene, are significantly lighter, but stronger and more resilient than traditional materials such as aluminium. Weight reduction is one of the easiest ways to improve efficiency in aircraft. Lower weight reduces the amount of energy (and therefore fuel) needed for take-off, climb and cruise. In addition, new composite materials can offer increased resistance to corrosion and fatigue, extending aircraft life and reducing maintenance costs.
The use of new composite materials also presents challenges, mainly related to investment in research and, further down the line, to feasibility and safety studies required by current regulations. Despite these challenges, the use of composite materials is increasing, and several modern aircraft models such as the Boeing 787 and the Airbus A350 already incorporate a high proportion in their structure. In addition, aerospace engineering is working to develop new, more aerodynamic designs that seek to reduce drag, which in turn reduces fuel consumption. Advances in computer simulation and wind tunnels have allowed engineers to design aircraft with much more efficient airfoils. Thinner wings and longer wingspans, combined with technologies such as the wingletswhich reduce induced drag, are very recent examples of such improvements. In addition, more aerodynamically shaped airframes and optimised control surfaces not only reduce fuel consumption, but can also increase cruise speed and improve aircraft load carrying capacity.
Some of the world's largest airlines have introduced major initiatives to reduce their emissions and are actively investing in different sustainable technologies. For example, Air France and KLM have launched several sustainability programmes, which include among other things upgrading their fleet with more fuel-efficient aircraft and implementing greener operating practices, such as the purchase and use of SAF fuels. British Airways is also committed to achieving a "zero emissions" target by 2050, investing in new fuel-efficient aircraft, optimising its flight routes and, like Air France and KLM, exploring the use of SAF. Across the Atlantic, Delta Air Lines has announced significant investments in carbon reduction technologies and emissions offset projects, as well as new research and development programmes for electric and hybrid aircraft. Beyond the airlines, several pioneering projects are emerging with the aim of revolutionising sustainable aviation. One of the most notable is the "Solar Impulse" project, an initiative that demonstrated the feasibility of flights powered entirely by solar energy. This project, led by Bertrand Piccard and André Borschberg, succeeded in circumnavigating the globe in a plane powered solely by solar energy, setting a precedent for the future of zero-emission aviation.
The transition to sustainable aviation is a monumental challenge that requires the collaboration of all scientists and researchers, the aviation industry - from aircraft manufacturers to airlines - technology investors and, perhaps most importantly, regulators and governments. Technological innovations in propulsion systems, such as electric and hybrid engines, coupled with advances in aircraft design and the use of sustainable fuels, offer a clear and very promising path towards emissions reductions and, eventually, even decarbonisation. However, for these solutions to be implemented effectively and on a large scale, robust policy incentives and regulations are essential. Government subsidies for the development and adoption of clean technologies, coupled with carbon taxes, can create an economic environment that favours sustainability in a competitive manner. In addition, international agreements and carbon offsetting schemes, such as the UN-driven CORSIA, are essential to ensure global and coordinated emission reductions. Ultimately, the combination of technological, operational and regulatory efforts will be key to achieving sustainable aviation, which meets global emissions targets.
A new platform to fly
If aviation were a country, it would rank among the top 10 global emitters of CO2, although in reality it accounts for only 2% of greenhouse gas emissions and a flight today generates half the CO2 in 1990. The industry has filed 40,523 technology patents for climate change mitigation since 1987, most of them in the category of efficient propulsion technologies, with the US clearly leading the way. But it is being asked, globally, to do something akin to real industrial conversion. ICAO (International Civil Aviation Organization) member states adopted the collective global long-term aspirational goal (LTAG) of achieving net zero carbon emissions by 2050. In parallel, a group of 25 airlines, representing more than 30% of global air passenger traffic, have already committed to the Science Based Target initiative to achieve net zero carbon emissions. In addition to the combined effects that increase the impact of their emissions, discussed in the previous chapter, the reason why aviation is under the sustainability spotlight has to do with expectations stemming from the forecast increase in air travel.
In the European Union, clean aviation is already seen as a central player linked to the global competitiveness of its economy, employing 13.5 million people (3.6% of all employment in Europe) and generating economic activity worth €1 trillion (4.4% of European GDP). The UK aviation industry has calculated that ICAO's 2050 net zero emissions target will require savings of almost 70 million tonnes of carbon dioxide (MtCO2). To achieve this, it relies on the coercive power that decarbonisation costs can have on demand if potential price increases are passed on to the market. These include operating costs associated with aircraft technology improvements aimed at reducing fuel consumption and cutting CO2 emissions by 30% to 40% compared to 2019. These are estimated at between $710 billion and $740 billion for airlines up to 2050, which will most likely lead to higher aircraft prices. There will also be costs to consider linked to the higher price of SAF (Sustainable Aviation Fuel), which the EU is subsidising, and the requirement to comply with global and regional carbon offsetting and trading schemes such as CORSIA and the EU's ETS2. Brussels' requirements in relation to the ETS will be tightened from 2030. EU airports will have to offer 2% of sustainable fuel in 2025 and increase that percentage every five years to reach 63% in 2050. It is part of an ambitious programme led by the Clean Aviation Joint Undertaking (CAJU) to develop new disruptive aviation technologies, in support of the European Green Pact and the goal of climate neutrality by 2050.
Europe wants a net reduction in greenhouse gas (GHG) emissions from aviation of no less than 30% by 2020. To achieve this, it envisages the deployment of new aircraft with net CO2 emissions up to 90% lower than today by 2035, so that 75% of the world's civil aviation fleet is replaced by 2050. The positions of the various administrations are not, however, homogeneous. Sweden, Norway and France have even more ambitious UAS plans than the EU, while the US has set a production target of only 11 billion litres per year by 2030 (California has opted out and wants to reach 20% of supply). The UK Department for Transport is part-funding a Virgin Atlantic-led project called Flight100 involving Imperial College London, Sheffield University, Boeing, Rolls-Royce, BP and others to demonstrate that PBS is an alternative to regular jet fuel. With an unpredictable willingness to lead in the new environment, Emirates, which successfully completed the first 100% demonstration flight powered by SAF, in partnership with Boeing and GE, has set up a $200 million fund, in line with the National Sustainable Aviation Fuel Roadmap launched by the UAE in 2023.
Over the next ten years, the industry will spend more than $50 billion on sustainable aviation projects.[xiii]. In the US, the Inflation Reduction Act includes hundreds of billions of dollars in incentives for low-carbon technologies, and that includes UAS and hydrogen production for the aviation sector. To estimate the scale of the challenge, the calculation made by British Aviation can be used as a reference: its projections to avoid the aforementioned 70 million MtCO2 emissions increase by 2050 if the 78% growth of its activity is confirmed and the scenario does not improve, are that, in addition to the progressive introduction of PAS, it will also be necessary to cut 2.5 MtCO2 through better air traffic management and operational procedures; 9.5 MtCO2 from the introduction of new versions of current aircraft and the emergence of more efficient design models; 10.6 MtCO2 from future aircraft types such as electric and hydrogen; 26.4 MtCO2 from the effect of sustainable aviation fuels; and 8.8 MtCO2 from permanent carbon removals.
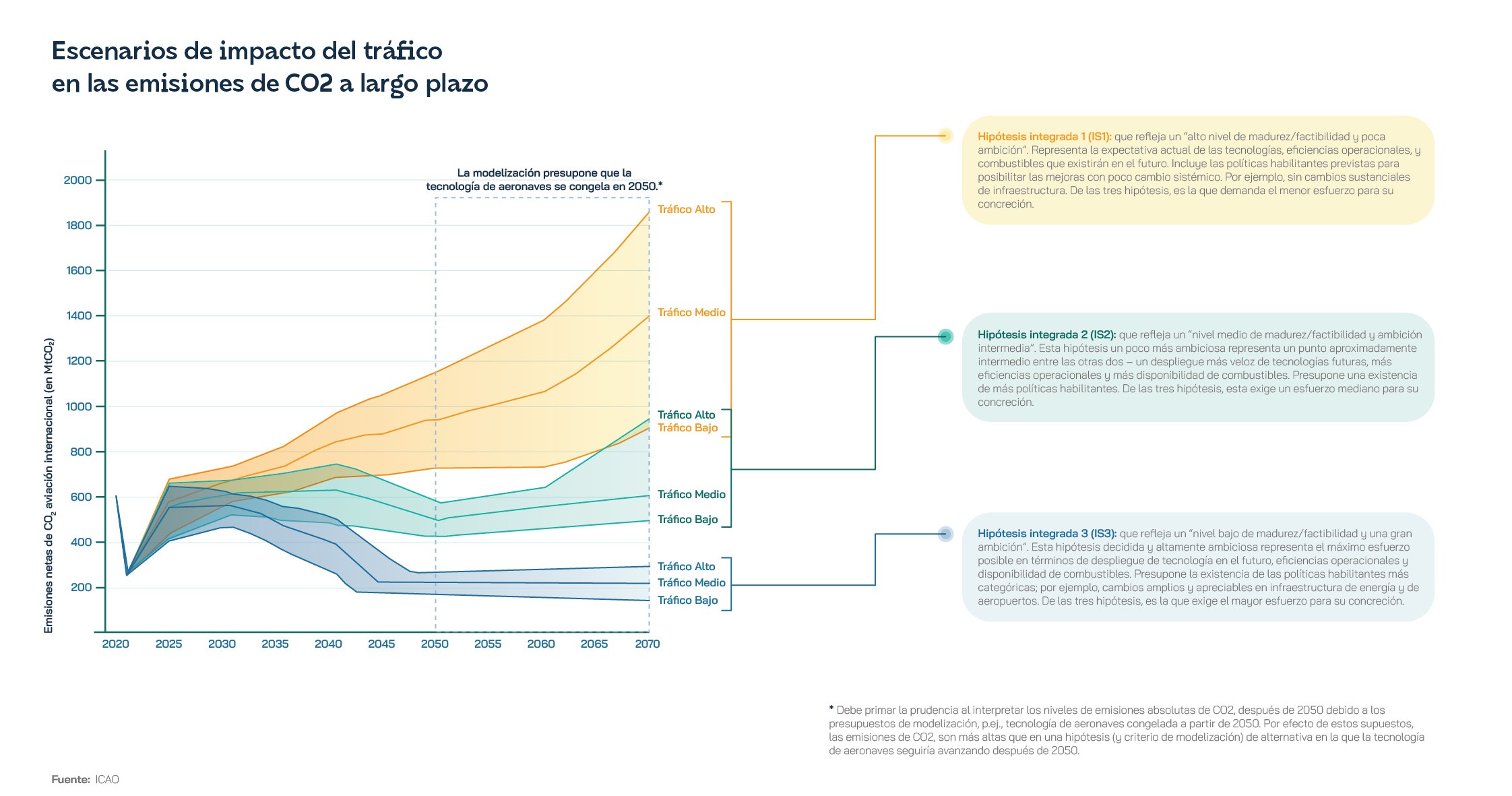
Strategic action must be taken on a large scale and involve all areas of government. It will need to ensure, for example, sufficient electricity generation and green hydrogen. Again in the UK, Sustainable Aviation forecasts that up to 147 TWh of additional renewable energy will be needed by 2050. The key point is that none of the solutions being considered achieve zero CO2 emissions through improvements in technologies, operations and fuels directly applicable to aviation, whether in aerodynamics, systems, structures, materials or propulsion. Collateral aspects related to the whole life cycle of each of these components and the overall traffic growth rate have to be considered. In that sense, considering the environmental impact of their production and distribution, not only their use to power aircraft engines, the expected net contribution of hydrogen in 2050 is reduced to only 1.9% in total energy.
In the last decade, advanced twin-aisle and long-range aircraft with significant improvements in all these critical sustainability technology areas, such as the Boeing 787-9 and -10, the Airbus A350-900 and 1000, and the Boeing B777-9 with composite wing, have entered service and undergone certification. The same has been true in the single-aisle segment, such as the Airbus A220-100 and -300, some with substantial propulsion and airframe technology improvements, such as the Airbus A320neo, A321XLR and A330neo, the Boeing B737MAX family and the Embraer EJets E2. All of these represent the state of the art in turbofan aircraft design and are benchmarks for developments taking place in countries such as China (C919), Japan (Spacejet) and Russia (MC21), and in the hangars of manufacturers such as Bombardier (Global 7500), Dassault (Falcon 8X) and Gulfstream (G650 and G700).[xv].
These moves demonstrate that there is much scope for innovation beyond fuel. For example, a significant reduction in lift-dependent drag can be achieved by increasing the effective wing span, as work at centres of excellence such as the Georgia Institute of Technology is demonstrating. Some manufacturers are pushing them to the limits specified by ICAO, introducing tip devices to increase the effective size while maintaining an acceptable payload, or enabling folding wing tip mechanisms for use on the ground so as not to create problems with existing airport infrastructure. The folding wing tip technology also favours the introduction of the hybrid wing body (HWB) which has no clear external boundary line with the main body of the aircraft, can have a tail and generally locates the propulsion system on the upper surface, which also allows noise reduction through acoustic shielding. Airbus included a HWB configuration on one of the three hydrogen-powered aircraft tested in its ZEROe programme. The potential entry into service of this technology is estimated to be in the 2035-40 timeframe and the estimated energy reduction would reach 5-15%. By adopting a load alleviation approach, an increase in wingspan can also be facilitated without a significant increase in weight. This involves introducing motion into wing-mounted control surfaces, such as ailerons and spoilers, using appropriate sensors and control parameters to limit the wing root bending moment.
To cope with viscous drag due to airfoil and surface friction, the highest in conventional aircraft, methods with robust microscale geometries are being developed, but their impact on fuel consumption is still barely 1-2%. This value can be increased by maintaining laminar flow in the forward areas of nacelles, wings and engine tails through well-balanced structural and aerodynamic designs, such as those proposed by the BLADE (Breakthrough Laminar Aircraft Demonstrator in Europe) project within the European Clean-Sky 2 programme. It has already conducted flight tests on an Airbus A340-300 with modified outer wings. Further progress will be needed, but they already envisage fuel consumption savings of up to 5% for larger aircraft.
In the battle against other sources of drag, such as shock waves, interference and adverse boundaries, the use of computational fluid dynamics (CFD) in the various stages of the aircraft design process is highlighted by increased computing power. It is possible to virtually model with increasing levels of physical fidelity at local and aircraft scale.[xxi]although progress derived from this technology is still concentrated at the cruise stage. In this field, active flow control (AFC), key to addressing aircraft interference and boundary layer phenomena, has made significant maturation steps in the last decade, including the achievements of Boeing's EcoDemonstrator programme and the activities in Europe of AFLoNext.
Structural mass reduction is another key parameter for improving fuel efficiency. Aircraft are replacing hydraulic and pneumatic systems with electric equivalents and, in the area of airframes, research is underway into new models, such as non-circular lifting airframes and the "flying V". These need to be closely monitored because wide-body aircraft generate 45% of the industry's emissions. Alongside this, weight savings will be achieved by addressing airframe materials, which consist of two main families: composites and metallic, in particular low-density alloys. Both can benefit from new welding technologies, for thermoplastic resins, bonding and stitching, which increase their strength. Large single-aisle and long-range twin-aisle B777 and A330 aircraft have mostly metallic primary structures, while the twin-aisle B787 and A350 have mostly composite primary structures. Additive layer manufacturing methods, graphene and bionic structural concepts, driven by improved computational simulation, also open the door to new, lighter-than-current material performance. Diehl Aviation's sidewall is a success story in this regard: it incorporates 9% of bio-based materials and achieves a 10% weight reduction compared to existing sidewall technologies. Finally, additive manufacturing opens up possibilities for a better optimised load-bearing design, while reducing weight compared to traditional components performing the same function. It has to pass the difficult test of certifications, but technologies such as carbon fibre injection from Spain's Reinforce3D make it possible to produce lighter but equally strong non-metallic aviation components with additive manufacturing.
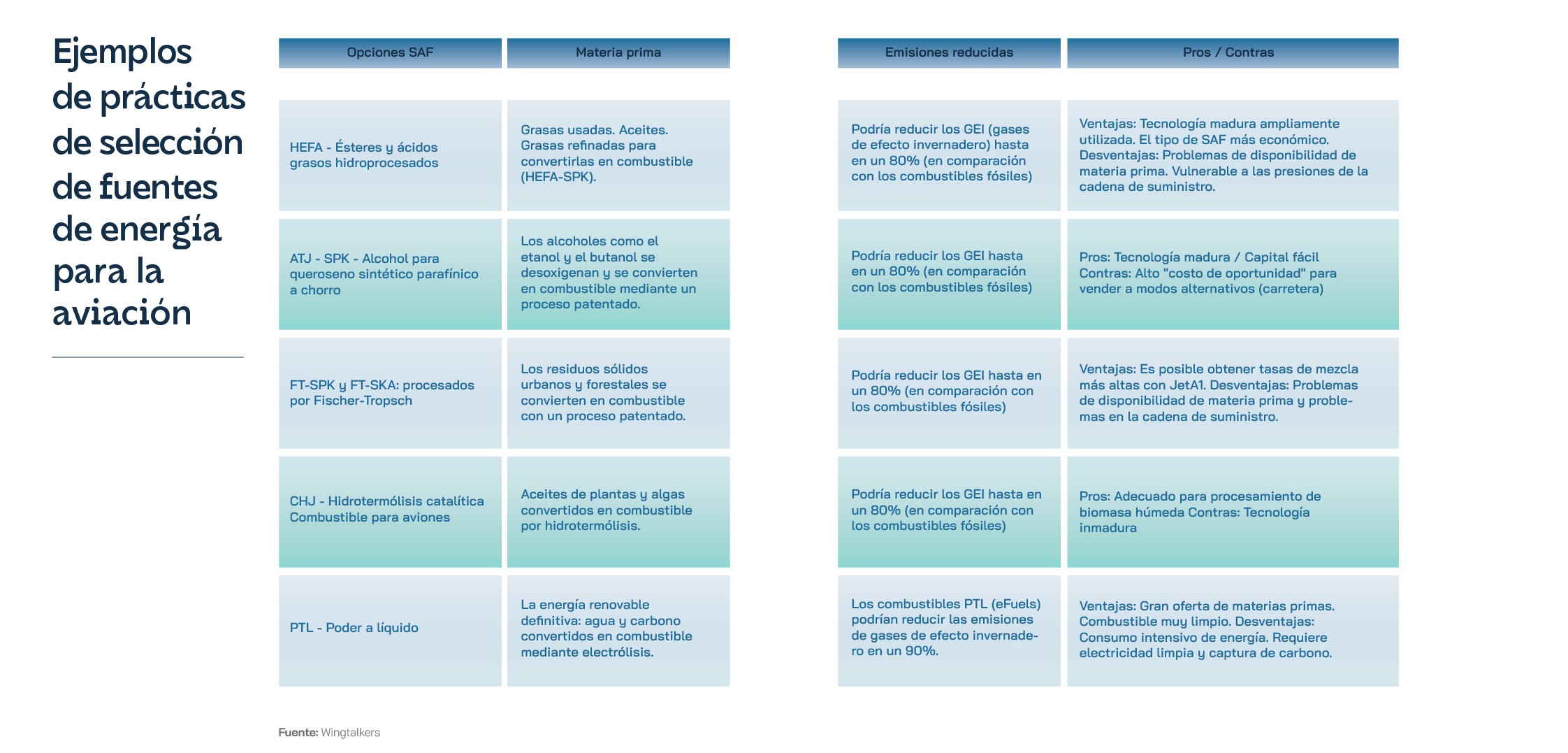
Improving thermal efficiency, which is already around 50-53%, is becoming increasingly difficult, even though it is key to minimising the deterioration of materials forced to operate at very high temperatures. Work is underway on turbomachinery technologies that mitigate current inefficiencies in high-temperature turbine operation and cooling, for which nickel superalloys and improved coatings have been developed to enable turbines to withstand 1700°C for many thousands of flight cycles. No further radical improvements are expected from this route, so the focus is shifting to ceramic matrix composites, which generally weigh less than their equivalent metallic components, and to new hot-section materials, such as eutectic ceramics and intermetallic alloys, which can operate at higher temperatures than superalloys. The problem with the latter is that they are not easily applied to rotating components such as discs, and therefore sealing and cooling technologies will be needed.
One area with great potential to improve efficiency is constant volume combustion. Since drag is proportional to the square of flight speed, it is proven that flying slower provides fuel savings and landing through a continuous descent at an airport saves at least 150 kg of CO2 per flight. At airports, work is in fact being done on so-called "green exits", which help planes take off and climb at a constant rate. Going from 1037 km/h to 864 km/h would allow a fuel saving of 13.1%, with the added bonus that 11.4 points of this saving is achieved at 913.7 km/h. The Subsonic Ultra Green Aircraft Research (SUGAR) study has pointed out that if the goal were to match NASA's fuel consumption ratios, the aircraft's cruise speed would have to be 740 km/h. But economic criteria have imposed a minimum speed of 864 km/h: flying slower would increase airlines' operating costs by reducing aircraft availability.
On the engine side, new energy sources will induce major changes in aircraft architectures, at least in the case of hydrogen-powered aircraft, which could be slower and operate over shorter distances by moving towards turboprop designs. Advanced conventional engines are ducted, such as Rolls-Royce's UltraFan, designed to meet the needs of the wide-body markets, which has set itself the challenge of achieving a fuel burn reduction of 20%, in its UltraFan H2 version. But a revolutionary alternative called the ductless fan or open rotor engine, which achieves higher load and cruise speeds than with propellers, is gaining momentum. Research has been underway in Europe and the US for decades, but it was the US-based CFM that first announced plans to demonstrate the technology as part of its integrated Revolutionary Innovation for Sustainable Engines (RISE) programme. Significantly, the first ground trials were initiated by the EU's Clean Sky programme, but a US company has managed to get a head start in the market. Its main visible drawbacks are blade containment, installation and cabin noise treatment, which will lead to a weight penalty in the aircraft, so it is not expected to be available before 2035.
As noted above, key constraints to scaling the electrified aircraft model include the power density of battery storage systems, which is approximately two orders of magnitude less than that of jet fuel, and the high weight of many components, as well as the effects of altitude or something as primary as ensuring a level of access to bulk electric power at airports. Creative solutions for aircraft battery storage are being investigated, including NASA's studies of multifunctional aircraft in which the airframe simultaneously serves as a battery, modifications that can help mitigate current limitations in terms of range, payload and speed.
When parked at the airport, aircraft must have power to provide air conditioning and electricity and also to start the engines, for which they are equipped with a small generator in the tail called an auxiliary power unit (APU). Many airports provide fixed electrical power on the ground and pre-conditioned air, so that pilots can turn off the APU while on the ground. Small all-electric or hybrid-electric aircraft, the option that will dominate initially, such as the E-Fan X being developed by Rolls-Royce, Airbus and Siemens, still show a huge dependence on synthetic fuels. They could be in service before 2035 and open the way for larger models from 2050 onwards.
As it becomes more widespread, new business models are emerging that will transform aviation: the American Ampaire is positioning itself in hybrid-electric aviation and by early 2024 had almost 30,000 kilometres flown; others, such as Canada's Azzera, offer a B2B software platform that enables airlines and governments to manage emissions. The European FUTPRINT50 project aims to accelerate electrification technologies for aviation by focusing on energy storage and harvesting and thermal management. It intends to deliver a hybrid-electric aircraft with up to 50 seats by 2035.
The fight for sustainability also has software as an ally. Artificial intelligence (AI) will be used to train pilots, provide better real-time flight data and predict customer booking patterns so that airlines can better manage resources. Will we continue to call them pilots, or, given the levels of autonomy of next-generation aircraft, should they redefine themselves as system operators? These are some of the questions being asked by the European Commission's SESAR Joint Undertaking 3 (SESAR-JU). One clear line of research seeks to exploit high-altitude weather conditions. Pilots and planners study wind patterns before departure and steer the aircraft into the currents more to reduce flight time and emissions. It has been shown that flights from New York to London could be up to 16.4% shorter and that current flight routes have air distances that are typically several hundred kilometres longer than those optimised with fuel. Potential air distance savings range from 0.7% to 7.8% when flying westbound and from 0.7% to 16.4% when flying eastbound.
Flexible routes are already used for long, uncrowded journeys, but new monitoring technology, similar to GPS, is gaining prominence for the most congested routes, while improving the design of the most appropriate flight paths to airports with difficult runway approaches, for example in mountainous areas. Such approach techniques can save millions of tonnes of fuel and CO2. Eurocontrol is promoting the use of AI within airports for tasks such as CO2-minimising runway allocation, the objective of a project initiated at Paris Charles de Gaulle airport, and optimising response times through machine learning. In the area of engineering, AI-assisted parametric design is revolutionising the field. The most advanced manufacturers, such as Airbus and Boeing, have complex simulation infrastructures and fully virtual test environment ecosystems that they use for the design phase, but also for verification and validation, for example to identify parts that can be changed less frequently without affecting confidence levels. The industry does not, however, remain unchallenged by the global IT talent gap.
Geographical and touristic interest in R&D
Spain's geographical position and the weight of tourism in its economy make the technological race for sustainable aviation a matter of the utmost strategic interest for the country. Despite this, the reaction of the main actors has been relatively recent. The National Integrated Energy and Climate Plan (PNIEC) 2021-2030 barely mentions the challenge when referring to the decisive contribution of biofuels to meeting the objectives of reducing the consumption of fossil fuels in the road transport and aviation sector. The plan proposes a specific boost to their production, which is still scarce due to the limited availability of some raw materials and the low level of technological maturity of some of the processes involved in the formation of biofuels.
As the first of the deadlines set by Brussels approached, especially with regard to the use of the PAS, the first moves have been made in regions where the aeronautical sector has a significant presence. The Madrid Vuela Sostenible project is a consortium led by Repsol, from its innovation centre, Technology Lab, located in Móstoles, in which the research centre of the Community of Madrid, IMDEA Energía, the technology SME Ariema and the startup Evoenzyme also participate. For their part, the Junta de Andalucía and the City Council of Jerez de la Frontera will collaborate in the creation of an aeronautical industry hub focused on sustainable aviation with the aim of attracting the interest of companies in the field of new fuels and maintenance, repair and operation activities.
In 2021, Iberia made the first flight in Spain with biofuel produced from waste at the Petronor refinery, and that same year Vueling did the same between Barcelona and Seville with SAF generated in Tarragona by Repsol from biomass. A year later, Iberia, in collaboration with Repsol, operated its first long-haul flights with this biofuel from Madrid to Washington, San Francisco and Dallas. Both companies are part of the All4Zero technological innovation hub. In July 2024, they reached an agreement for the supply of more than 28,000 tonnes of PBS, the largest purchase of this product to date in Spain. As of February of that year, the group had secured a third of the PBS needed to meet its target of using 10% of sustainable fuel by 2030.
The presence in our country of a powerful base of companies supplying components to Airbus and, to a lesser extent, Boeing has consolidated a layer of technology centres with advanced levels of research in the field of new alternative materials to metal for sustainable aviation. The AIMPLAS Plastics Technology Institute, together with Tekniker, has created a novel methodology for the end-of-life treatment of these materials within the European SPARTA project. Its process addresses the recycling and subsequent manufacture of thermoplastic composites such as high-performance polyetheretherketonacetone (PEKK) reinforced with continuous carbon fibre, by automatic deposition and reprocessing through compression moulding.
In Castilla y León, the technology centres CIDAUT and CTME have developed the interesting COMP_COAT project, together with the companies Aciturri Engineering and MPB Aerospace, both from the aerospace sector, aimed at improving the properties of composite materials and technical plastics by applying thermal projection technology, which involves ceramics and metals, on the surface. They have analysed properties such as resistance to temperature, wear and erosion, surface electrical conductivity, biocompatibility, and long-lasting UV protection, among others. As a result of the project, different processes have been developed to improve the functionalities of composites and technical plastics by thermal spraying with applications in various industrial sectors.